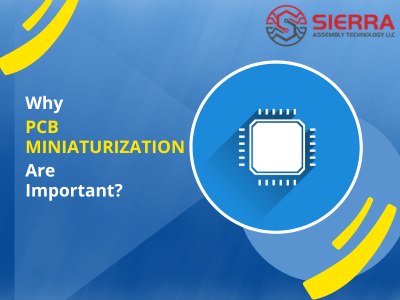
Miniaturization in PCB (Printed Circuit Board) refers to the process of designing and manufacturing electronic circuits with smaller components and reduced physical dimensions. The primary objective of miniaturization is to increase component density on the PCB, reduce the overall size and weight of electronic devices, and enhance their functionality while maintaining or improving performance.
Miniaturization involves the creation of smaller and more compact electronic devices through design and manufacturing. As the demand for highly portable devices grows, electrical engineers are confronted with the task of developing miniaturized printed circuit boards (PCBs) that can fulfill the technical requirements of these devices.
Why PCB Miniaturization or Mini PCB are Important?
Miniaturization in PCB design and manufacturing is a driving force behind the development of modern electronics. Mini circuit board enables the creation of smaller, more powerful, and feature-rich devices that are essential in meeting the demands of a rapidly evolving technological landscape.
Miniaturization is crucial in PCB (Printed Circuit Board) design and manufacturing for several important reasons:
-
Space Efficiency: Miniaturization allows electronic components to be packed closer together, optimizing the use of space on the PCB. This results in smaller PCB footprints, which is essential for applications where size and weight constraints are critical, such as in portable devices, wearables, and aerospace systems.
-
Compact and Lightweight Devices: Miniaturization enables the creation of compact and lightweight electronic devices. This is particularly beneficial for consumer electronics, automotive applications, and IoT (Internet of Things) devices, where smaller form factors are preferred for better user experience and convenience.
-
Enhanced Functionality: By reducing the size of components and increasing the component density on the PCB, miniaturization allows for the integration of more features and functionalities into electronic devices. It enables designers to add advanced capabilities and improve performance without increasing the device's overall size.
-
Higher Performance: Miniaturization can lead to shorter signal paths and reduced parasitic effects, improving signal integrity and reducing signal losses. This results in better high-speed performance, reduced electromagnetic interference (EMI), and overall enhanced PCB performance.
-
Energy Efficiency: Smaller components often consume less power, leading to increased energy efficiency in electronic devices. This is especially important for battery-powered devices where power consumption directly impacts battery life.
-
Cost Savings: Miniaturization can lead to reduced material costs, as smaller components require fewer raw materials. Additionally, mini circuit board may lead to more efficient manufacturing processes, resulting in cost savings during production.
-
Advancements in Technology: Miniaturization drives advancements in semiconductor and packaging technologies. As electronic components become smaller and more powerful, new innovations and applications become possible, leading to a continuous cycle of technological advancement.
-
Improved Design Flexibility: Smaller components and higher component density provide designers with more flexibility in PCB layout and design. This allows for more intricate and efficient routing of traces, leading to improved signal integrity and overall PCB performance.
-
Industry and Market Demands: Consumers and industries are increasingly demanding smaller and more powerful electronic devices that are easy to carry, use, and integrate into various systems. Miniaturization helps meet these demands and stay competitive in the market.
-
Applications in Emerging Technologies: Miniaturization plays a crucial role in emerging technologies such as wearable devices, medical implants, and Internet of Things (IoT) sensors. These technologies require tiny, low-power electronic components to operate seamlessly in their respective applications.
Factors to Consider for PCB Miniaturization
When pursuing PCB miniaturization, several critical factors need to be considered to ensure the success of the design and manufacturing process. These factors include:
-
Component Size and Packaging: Choose smaller surface-mount components with compact form factors to reduce the overall footprint of the PCB. Consider using chip-scale packages (CSPs) and ball grid arrays (BGAs) for integrated circuits to maximize component density.
-
Trace Width and Spacing: Decrease trace widths and spacing between traces to accommodate the reduced size of components and optimize signal routing while maintaining signal integrity.
-
Layer Count: Evaluate the necessity of additional PCB layers to accommodate the increased component density. Using more layers may allow for better routing and reduced signal crosstalk.
-
Thermal Management: As components are packed more closely, effective thermal management becomes critical. Plan for proper heat dissipation and consider the use of heat sinks or thermal vias to prevent overheating.
-
Power and Signal Integrity: Ensure that the reduced size of the PCB does not compromise power distribution and signal integrity. Conduct simulations and analyses to verify the PCB's electrical performance.
-
Manufacturability: Evaluate the feasibility of manufacturing the miniaturized PCB design. Consider the capabilities of the PCB fabrication and assembly processes and ensure that the design is manufacturable at scale.
-
Assembly Techniques: Opt for automated assembly processes, such as pick-and-place machines, to accurately place small components on the PCB with high precision and reliability.
-
Material Selection: Choose PCB materials with good thermal conductivity and electrical properties, suitable for miniaturized designs. Advanced materials may be required to meet the demands of reduced form factors.
-
Environmental Considerations: Assess the operating environment of the electronic device to ensure the miniaturized PCB can withstand temperature variations, humidity, and potential exposure to chemicals or moisture.
-
Reliability and Testing: Conduct thorough testing and validation of the miniaturized PCB to ensure its reliability and functionality under real-world conditions. Implement testing techniques such as boundary scan testing or X-ray inspection to identify potential defects.
-
Cost and Scalability: Analyze the cost implications of miniaturization and assess whether the benefits outweigh the additional expenses. Consider the scalability of the design for mass production.
-
Regulatory Compliance: Verify that the miniaturized PCB design complies with relevant industry standards and regulatory requirements to ensure its safe and legal use in the intended application.
Future of PCB Miniaturization
The future of PCB miniaturization is dynamic and will continue to evolve with technological advancements and market demands. As technology advances and demands for smaller, more powerful, and portable devices increase, PCB miniaturization will remain a key trend. It will shape the development of smaller, smarter, and more interconnected electronic devices, revolutionizing industries and enhancing the way we interact with technology in our daily lives.