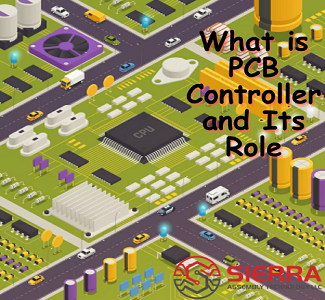
A PCB controller refers to a microcontroller or a dedicated integrated circuit (IC) that is responsible for controlling and managing the operations of a printed circuit board (PCB). It serves as the brain of the system, providing intelligence, decision-making capabilities, and interface functionalities.
What is the difference between controller and PCB?
A controller and a PCB (Printed Circuit Board) serve different purposes and play distinct roles in an electronic system. Here's an explanation of the differences between the two:
PCB (Printed Circuit Board):
A PCB is a physical board made of non-conductive material (such as fiberglass or epoxy) that provides mechanical support and electrical connections between various electronic components. It is designed to host and interconnect different electronic components, such as integrated circuits (ICs), resistors, capacitors, and more.
The main functions of a PCB are:
-
Providing a platform for mounting electronic components.
-
Creating electrical pathways or traces to establish connections between components.
-
Distributing power and signals throughout the board.
-
Ensuring proper grounding and shielding.
-
Facilitating the efficient flow of electrical current.
Controller:
A controller, on the other hand, refers to a device or a component responsible for controlling and managing the operations of a system. It can be a microcontroller (MCU), a microprocessor, a programmable logic controller (PLC), or a dedicated integrated circuit (IC) specifically designed for control purposes.
The main functions of a controller are:
-
Processing data and executing instructions.
-
Controlling and coordinating the behavior of the system.
-
Receiving input signals, processing them, and generating output signals.
-
Implementing control algorithms or logic.
-
Managing interfaces and communication with other devices or systems.
Controllers are typically programmed to perform specific tasks and are responsible for making decisions, executing commands, and regulating the operation of the system based on input data.
The Main Tasks of a PCB Controller Include:
1. Data processing: The controller receives input signals from sensors, switches, or other external devices connected to the PCB. It processes and analyzes this data to make decisions or perform specific actions.
2. Signal management: The controller handles the routing and distribution of signals within the PCB. It ensures that signals are properly transmitted and received between different components and modules on the board.
3. Control logic: The controller executes specific control algorithms or logic to regulate the behavior of the PCB. This may involve managing power distribution, controlling actuators or motors, adjusting sensor readings, or implementing communication protocols.
4. Memory and storage: Many PCB controllers have built-in memory or storage capabilities to store program code, configuration settings, and data. This allows them to retain information even when power is disconnected.
5. Interface management: The controller often provides various interfaces to interact with external devices or systems. These interfaces can include digital and analog input/output pins, serial communication ports (such as UART, SPI, or I2C), Ethernet or USB ports, and wireless connectivity options (like Wi-Fi or Bluetooth).
Overall, a PCB controller plays a crucial role in coordinating and managing the functionality of a PCB, enabling it to perform its intended tasks efficiently and effectively.
What are the Dimensions of PCB Controller?
The dimensions of a PCB controller can vary depending on the specific design and requirements of the electronic system it is used in. There is no standard size or dimension for a PCB controller as it can be designed to fit various form factors and applications.
The size of a PCB controller is determined by several factors, including:
1. Integration level: The size of the controller can be influenced by the level of integration and the number of components incorporated into the controller. More complex controllers with additional features may require larger dimensions.
2. Package type: The package type of the integrated circuit used for the controller can also impact its dimensions. Different package types, such as quad flat packages (QFP), ball grid arrays (BGA), or chip-scale packages (CSP), have varying sizes and footprints.
3. System requirements: The dimensions of the PCB controller may be influenced by the physical constraints of the system it is intended for. The available space in the device or equipment housing will dictate the maximum size of the controller.
4. Design considerations: The designer's priorities, such as optimizing space utilization or accommodating additional peripherals, can also influence the dimensions of the PCB controller.
How to Design PCB Controller?
Designing a PCB controller involves several steps and considerations. Here is a general overview of the process:
1. Define the Requirements: Clearly define the requirements and specifications of the PCB controller. Understand the purpose, functionality, input/output requirements, power considerations, and any specific constraints or standards that need to be followed.
2. System Architecture: Determine the overall system architecture and identify the key components and their interconnections. This includes selecting the microcontroller or dedicated IC for the controller based on the requirements.
3. Schematic Design: Create a schematic diagram that represents the circuit connections and components of the PCB controller. Place the selected microcontroller and other components such as power supply, memory, interfaces, sensors, etc., on the schematic.
4. PCB Layout: Transfer the schematic design to the physical layout of the PCB. Place the components in their desired locations, considering factors such as signal integrity, power distribution, and thermal management. Route the traces to establish the necessary connections between components while adhering to design rules and constraints.
5. Power and Ground Planes: Design appropriate power and ground planes to ensure stable power distribution and noise reduction. These planes provide low impedance paths for power supply and serve as a reference for signals.
6. Signal Integrity: Pay attention to signal integrity by considering trace impedance, controlled impedance routing, minimizing signal coupling, and managing high-speed signals with proper termination and signal integrity techniques.
7. Component Placement: Optimize component placement for signal integrity, thermal considerations, and ease of assembly. Group related components together and consider their proximity to reduce trace lengths and noise coupling.
8. PCB Design Rules: Define design rules such as minimum trace width, spacing, clearance, and other manufacturing constraints to ensure manufacturability and reliability.
9. Gerber Files and Manufacturing Documentation: Generate Gerber files, which are industry-standard files that describe the
PCB design layers, for manufacturing. Create assembly drawings, bill of materials (BOM), and other documentation required for manufacturing and assembly.
10. Prototype and Testing: Once the PCB design is complete, manufacture a prototype for testing and validation. Conduct
functional testing, verify the performance, and make any necessary revisions to the design if required.
11. Production: Once the design has been thoroughly tested and validated, proceed with mass production of the PCB controller. Work with a reliable PCB manufacturer to ensure high-quality production.
It's important to note that PCB design is a complex process, and expertise in electronics, circuit design, and PCB layout software is recommended. Additionally, consider consulting with experienced PCB designers or engineers to ensure the success of your PCB controller design.
Materials Used in PCB Controller
A PCB controller, like any other printed circuit board (PCB), can be
composed of various materials depending on the specific requirements of the design. Here are some common materials used in the construction of PCB controllers:
1. Substrate Material:
-
FR-4: This is the most widely used substrate material for PCBs. It is a flame-retardant fiberglass epoxy laminate that provides good electrical insulation and mechanical stability.
-
High-Temperature FR-4: Similar to FR-4, but designed to withstand higher operating temperatures.
-
Rogers: Specialized high-frequency PCBs may use Rogers substrates, which offer low dielectric loss and excellent signal performance at high frequencies.
2. Copper Foil: Copper is used to create conductive traces and pads on the PCB. The copper foil is typically laminated onto the substrate material and comes in different thicknesses, such as 1 oz or 2 oz (ounces per square foot).
3. Solder mask: Solder mask is applied to the PCB to protect the copper traces from oxidation and to provide insulation between traces. It is typically made of epoxy-based materials, such as green, red, blue, or black solder mask.
4. Silkscreen: The silkscreen layer is used to print component labels, part numbers, and other identifying information on the PCB. It is typically printed using white or black ink.
5. Surface Finish:
-
HASL (Hot Air Solder Leveling): A common surface finish that involves coating the exposed copper with a layer of tin-lead solder.
-
ENIG (Electroless Nickel Immersion Gold): A surface finish that provides good solderability, corrosion resistance, and flatness.
-
OSP (Organic Solderability Preservative): A thin protective layer that prevents oxidation of the copper traces before PCB assembly.
6. Solder Paste: Solder paste is used for attaching components to the PCB during the assembly process. It is a mixture of flux and tiny solder particles.
7. Components: PCB controllers incorporate various electronic components, such as microcontrollers, integrated circuits, resistors, capacitors, inductors, connectors, and more. These components have their own specific materials, including silicon for integrated circuits, ceramic for capacitors, and various metals for connectors and leads.
It's important to note that the choice of materials depends on factors such as the application, environmental conditions, thermal management requirements, signal integrity, and cost considerations.
What is The Role of PCB Controller?
The role of a PCB controller is crucial in electronic systems as it serves as the central component responsible for controlling and managing the operations of the system. Here are the key roles of a PCB controller:
-
Data Processing: The PCB controller receives input signals from various sources such as sensors, switches, or other external devices. It processes and analyzes this data to make decisions or perform specific actions based on predefined algorithms or logic.
-
System Control: The controller regulates and coordinates the behavior of the system by executing control algorithms. It manages the flow of data, commands actuators, adjusts parameters, and monitors the system's performance to achieve the desired functionality and operation.
-
Interface Management: The controller provides interfaces to interact with external devices or systems. These interfaces can include digital and analog input/output pins, serial communication ports (such as UART, SPI, or I2C), Ethernet or USB ports, wireless connectivity options (like Wi-Fi or Bluetooth), and other specialized interfaces required for the system's functionality.
-
Memory and Storage: Many PCB controllers have built-in memory or storage capabilities to store program code, configuration settings, and data. This allows them to retain information even when power is disconnected. The controller manages memory access and storage operations.
-
Signal Management: The controller handles the routing and distribution of signals within the PCB. It ensures that signals are properly transmitted and received between different components and modules on the board, managing factors such as signal integrity, noise reduction, and impedance matching.
-
Power Management: In many cases, the PCB controller is responsible for managing the power distribution and supply to various components and subsystems of the electronic system. It regulates power levels, monitors voltage/current levels, and may implement power-saving techniques to optimize energy consumption.
-
System Monitoring and Fault Detection: The controller monitors the system's operation, including parameters, sensor readings, and performance metrics. It detects faults or abnormal conditions and triggers appropriate responses, such as generating alerts, activating backup systems, or initiating corrective actions.
-
Communication and Networking: The controller facilitates communication and networking capabilities, enabling the system to interact with other devices, exchange data, and connect to external networks. It may support protocols like Ethernet, CAN (Controller Area Network), wireless protocols, or custom communication protocols.
Overall, the PCB controller plays a pivotal role in overseeing and coordinating the operation of an electronic system. It combines computational capabilities, control logic, and interfaces to enable the system's desired functionality, responsiveness, and reliability.