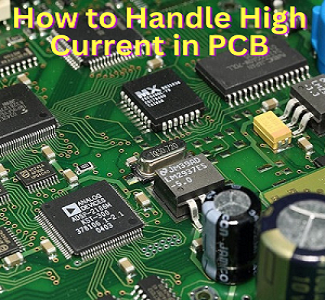
A printed circuit board (PCB) is a fundamental component in electronic devices and systems. It provides a platform for interconnecting and supporting various electronic components to create functional circuits. PCBs are vital components in electronic devices, enabling efficient component integration, electrical connections, miniaturization, signal integrity, reliability, and manufacturing efficiency.
What is High Current PCB?
A high current PCB refers to a printed circuit board that is specifically designed to handle and carry high levels of electrical current without experiencing significant voltage drops or overheating. These
types of PCBs are commonly used in applications that require the transmission of large currents, such as power supplies, motor controllers, automotive electronics, industrial equipment, and high-power LED lighting systems.
Design and Construction of a High Current PCB
The design and construction of a high current PCB involve several considerations to ensure optimal performance and reliability. Here are some key features and techniques used in high current PCB design:
-
Copper Trace Width and Thickness: High current PCBs typically feature wider copper traces to reduce resistance and accommodate the flow of larger currents. Increasing the copper thickness, measured in ounces per square foot, can also help lower resistance and improve current-carrying capacity.
-
Copper Pour and Planes: To further enhance current-carrying capacity and thermal dissipation, high current PCBs often employ copper pours or planes. These large areas of copper, connected to power and ground, help distribute the current evenly and reduce the chances of overheating.
-
Thermal Management: High currents generate heat, and proper thermal management is crucial to prevent excessive temperature rise on the PCB. Techniques such as heat sinks, thermal vias, and strategically placed copper pours can help dissipate heat efficiently.
-
PCB Substrate Material: The choice of substrate material is important for high current PCBs. Materials with high thermal conductivity and good electrical insulation properties, such as specialized high-temperature FR-4 or metal core PCBs, are often preferred.
-
Through-hole Technology (THT): High current PCBs may use through-hole components instead of or in addition to surface-mounted components. Through-hole components offer robust mechanical connections and can handle larger currents compared to their surface-mounted counterparts.
-
Soldering Techniques: High current PCBs may require specialized soldering techniques, such as wave soldering or selective soldering, to ensure reliable and strong electrical connections capable of carrying high currents.
-
Design Considerations: High current PCB design requires careful consideration of trace widths, copper thickness, trace lengths, and signal integrity. Minimizing the length and resistance of traces carrying high currents, avoiding sharp corners, and optimizing the layout to reduce voltage drops are essential for efficient performance.
It's important to note that the specific design requirements and techniques for high current PCBs may vary depending on the application and current levels involved.
What Happens if Current is too High in PCB?
If the current flowing through a PCB (Printed Circuit Board) exceeds its designed capacity or maximum rated current, several issues can occur, potentially leading to various consequences:
-
Overheating: Excessive current generates heat due to resistive losses in the PCB traces and components. If the current surpasses the PCB's capability, it can result in excessive heating, potentially causing damage to the board and its components. Overheating can lead to component failure, reduced lifespan, and overall system malfunction.
-
Voltage Drops: High currents passing through PCB traces with inadequate width or excessive resistance can cause significant voltage drops along the path. Excessive voltage drops can lead to underpowered or unstable operation of components, affecting their performance or causing them to malfunction.
-
Signal Integrity Issues: Excessive current flowing through PCB traces can induce electromagnetic interference (EMI) and create noise that interferes with signal integrity. This can lead to communication errors, data corruption, or signal degradation, impacting the overall functionality and reliability of the circuit.
-
PCB Damage: The excessive current can physically damage the PCB, particularly the traces that are unable to handle the high current levels. The increased current density can result in trace delamination, trace lifting, or even the burning of the PCB substrate. This can lead to open circuits, short circuits, or complete failure of the affected sections.
-
Component Failure: Components themselves may not be designed to handle high currents beyond their specified ratings. The excessive current can cause components to heat up, exceed their maximum temperature limits, and potentially result in component failure or reduced reliability.
-
Safety Hazards: High currents flowing through a PCB can pose safety risks, including the risk of electrical shock, fire, or damage to other system components. The excessive current can lead to the overheating of connectors, terminals, or other electrical interfaces, increasing the likelihood of short circuits or electrical faults.
To prevent these issues, it is crucial to carefully design the PCB, considering the expected current levels, trace widths, copper thickness, thermal management, and component selection.
Component Selection for High Current PCB
When designing a high current PCB, selecting the right components is crucial to ensure the circuit can handle the desired current levels effectively. Here are some key considerations for component selection in high current PCB designs:
-
Power Devices: Choose power devices (such as MOSFETs, IGBTs, or power transistors) that have a high current rating and low on-resistance. Look for devices specifically designed for high current applications and check their datasheets for relevant parameters such as maximum current, voltage rating, and thermal characteristics.
-
Connectors: Select connectors that are rated for high currents and have low contact resistance. Consider connectors with larger contact areas, multiple pins for parallel current paths, and appropriate wire gauge compatibility. High current connectors may include power connectors, terminal blocks, or heavy-duty connectors.
-
Capacitors and Inductors: Choose capacitors and inductors with sufficient current ratings to handle the expected currents without significant losses. Consider low equivalent series resistance (ESR) capacitors and low direct current resistance (DCR) inductors to minimize power dissipation and voltage drops.
-
PCB Mounting: Ensure that the chosen components are suitable for the selected PCB mounting method, whether it is surface mount technology (SMT) or through-hole technology (THT). Verify that the components can handle the required current levels in the selected mounting configuration.
-
Heat Sink Compatibility: If power devices require heat sinks for thermal management, select components that are compatible with the chosen heat sink solution. Check for appropriate mounting options and thermal resistance specifications to ensure efficient heat dissipation.
-
Thermal Considerations: Consider components with thermal characteristics that match the requirements of the high current application. Look for components with low thermal resistance and thermal shutdown protection, if applicable.
-
Voltage Ratings: Verify that the selected components have voltage ratings that exceed the anticipated voltage levels in the circuit. High current circuits often involve high voltages, and component selection should account for these voltage requirements.
-
Reliability and Longevity: Consider the reliability and longevity of components in high current applications. Look for components from reputable manufacturers with a proven track record in high current designs. Consider factors such as component lifespan, derating curves, and reliability specifications.
-
Design for Manufacturing (DFM): Ensure that the selected components are readily available and suitable for cost-effective manufacturing. Components that are widely used and readily sourced will help streamline the production process and ensure a stable supply chain.
-
Consult Component Datasheets: Thoroughly review the datasheets of selected components to gather all the necessary information regarding their current ratings, thermal characteristics, voltage ratings, and other relevant specifications.
It's important to note that the specific component selection will depend on the unique requirements of your high current application.
Benefits of High Current Heavy Copper PCBs
High current heavy copper PCBs offer several benefits and advantages compared to standard PCBs. Here are some of the key benefits of using high current heavy copper PCBs:
-
Increased Current Carrying Capacity: Heavy copper PCBs are designed to handle high currents and can carry significantly more current compared to standard PCBs. The increased copper thickness allows for lower resistance, reduced voltage drops, and improved current-carrying capability.
-
Enhanced Thermal Management: High current applications generate heat, and heavy copper PCBs provide improved thermal management capabilities. The increased copper mass acts as a heat sink, spreading and dissipating heat more effectively. This helps in maintaining lower operating temperatures, reducing the risk of component overheating and improving overall system reliability.
-
Improved Power Distribution: Heavy copper PCBs offer better power distribution characteristics, especially in applications where power needs to be distributed to multiple components or subsystems. The increased copper thickness ensures a more uniform distribution of power, minimizing voltage drops and improving overall power efficiency.
-
Higher Durability and Mechanical Strength: The additional copper weight in heavy copper PCBs enhances their mechanical strength, making them more resistant to mechanical stress, bending, and vibration. This makes them suitable for applications that require robust and durable PCBs, such as industrial equipment, automotive systems, and power electronics.
-
Increased Design Flexibility: Heavy copper PCBs provide greater design flexibility due to their higher current carrying capacity. Designers can use wider traces, larger vias, and thicker copper layers to accommodate the specific requirements of high current applications. This allows for more compact designs, reduced layer counts, and improved overall PCB layout efficiency.
-
Improved Electrical Performance: Heavy copper PCBs exhibit lower resistance and impedance, resulting in improved electrical performance. This can help reduce signal loss, minimize voltage fluctuations, and improve signal integrity, especially in high-speed or high-frequency applications.
-
Cost and Space Savings: While heavy copper PCBs may have a higher initial manufacturing, cost compared to standard PCBs, they can provide cost savings in the long run. Their ability to handle higher currents allows for the use of smaller and more cost-effective components, reducing overall system costs. Additionally, their increased current carrying capacity can enable PCB size reduction, saving valuable space in compact electronic devices.
-
Wide Range of Applications: Heavy copper PCBs find applications in various industries and sectors that require high power handling, such as power supplies, motor controllers, renewable energy systems, electric vehicles, aerospace, and telecommunications, among others.
It's important to note that designing and manufacturing heavy copper PCBs may require specialized fabrication techniques and expertise.